News
In-situ strength assessment, EN 13791
EN 13791 and its complementary Technical Report TR 17086 Further guidance on the application of EN 13791.2017 and background to the provisions have been published for CEN Enquiry/vote, where votes and comments are required by 4 April 2017.
Conformity - European Standard for Concrete, EN 206
Austria raised a formal objection to the European Standard for Concrete, EN 206, in that breaks the neutrality principle. That is all documents containing requirements for products shall be written such that conformity can be assessed by a user (second party) or an independent body (third party) as well as a producer (first party). ERMCO have re-activated their Technical Committee on Conformity to facilitate European ready-mixed concrete discussion in preparation for the European Technical Standard Committee meeting set for 22 May 2017. Richard P Kershaw of CEMEX and Chris A Clear of BRMCA have agreed to participate in the ERMCO Working Group, ETC WG4.
Tom A Harrison and durability testing
After many years as Convenor of CEN TC51/TC104 JWG/12 TG5 Durability test methods Tom Harrison is standing down, Chairing his last meeting on 19 January 2017 at BSI Chiswick. All the Committee members expressed their sincere thanks to Tom for his very hard work in always ensuring consensus for a Group that likes to spend a lot of time considering technical details.
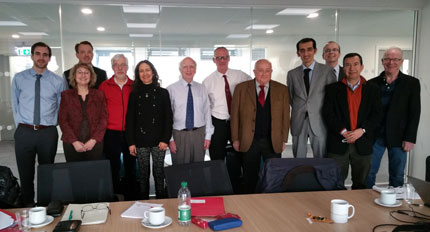
Left to right: Colum McCague, Carmen Andrade, Knut O Kjellsen, Joost Gullickers, Veronique Baroghel-Bouny-new Convenor, Tom A Harrison, Chris A Clear, Stefano Congiano, Antonio Princigallo, Moray Newlands-Secretary, Miguel Climent, Steinar Helland
Gallagher Ashford
On 10 February 2017 Gallagher Aggregates opened a totally new ready-mixed concrete plant at Ashford in Kent. At the heart of the Total Batching Solutions’ bespoke plant is a 2m3 Pemat pan mixer that can mix the concrete to discharge into a ready-mixed concrete truck. The high speed of the process provides a daily capacity of up to 800m3 per day. In addition, the plant can accommodate customer collections through a specially designed chute.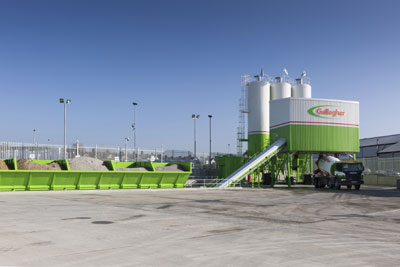
Aggregates are weigh batched from four ground level 50 tonne bins, and elevated to the mixer by fully enclosed conveyors for safety and dust suppression. The moisture content of the fine aggregates is continuously monitored by moisture meters, where the mass of the moist aggregate is automatically corrected to ensure a stable content by dry mass. Limestone coarse aggregate and marine sand fine aggregate are sourced locally in Kent.
Cementitious powders are stored in two 85 tonne silos and supplied via a weigh hopper to the mixer unit. The plant can also produce anhydrite flowing screed where a designated silo supplies to a separate weigh hopper to ensure there is no cross contamination with cementitious powders used for concrete.
The plant also has wash-out facilities that enable the recover and re-use of aggregates and water. The use of recycled water may be restricted to any percentage of total added water to comply with user specifications. |